Valve digital services
Maximizing valve performance and simplifying installed base management
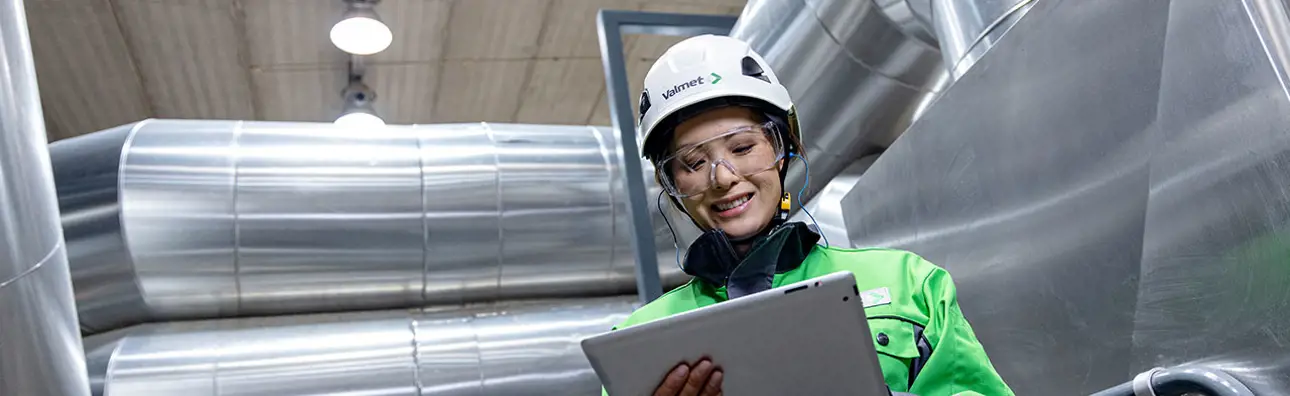
What is the current condition of my valve? What valves should I remove to repair? Why this valve is not performing well? Our flow control digital services offer solutions to your commonly asked questions. Valmet Valve Performance Monitoring maximizes plant reliability by predicting and preventing valve-related issues.
Maximize reliability
Minimize unplanned downtime, extend valve life and improve valve performance.
Reduce risk
Improves health, safety and environmental results
Reduce Total Cost of Ownership (TCO)
Focus maintenance resources, low cost, OpEx model
Improve valve performance
Valve data helps predict and prevent valve issues
Our service offering
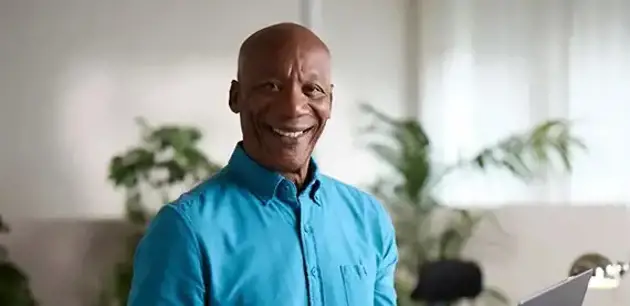
Valmet customer portal
Valmet Customer Portal is a custom tailored one-stop shop, where we provide you visibility to the full collaboration with Valmet. In addition to many other features, Valmet Customer Portal offers Asset Management where you can find your valves in your installed base. From the data you can find installed devices, their service history, spare parts, recommendations, documentation and more. With this information you can find valves that needs service and plan your maintenance actions based on data.
DiscoverValve performance monitoring
Valmet's valve performance monitoring service detects valves, which performance has degraded. This can disturb the process to create a foundation for efficient maintenance planning and action prioritization. Our Valve performance monitoring maximizes plant reliability by predicting and preventing valve-related issues.
The key benefits of VPM service are: minimized unexpected downtime, significant repair cost reductions with smarter maintenance planning, energy savings, valve wear reductions and increased product quality, as well as improved safety and communication in maintenance operations.
DMS agreement
Our Device Maintenance Solution (DMS) service is a comprehensive warehousing and maintenance solution to increase plant uptime and valve availability. With this service, all you critical valve products are covered by a stock of required components and spare parts to optimize availability. A predictive maintenance model maximizes plant reliability and uptime from valve products point of a view.
The extensive service also includes an installed base harmonization program and valve repair service. We guarantee fast response times to unplanned shutdowns and our stock management enables fast replacement service for the agreed stocked valves. The stock levels and items are developed continuously.
In addition, we can offer our expert, a Resident technician, to guide and support you on site.
Inventory management
With our vast knowledge of installed base, we are able to use advanced analytics to create inventory recommendations based on the valves and other flow control devices installed at your site. The advanced analytics are based on AI service demand model and also takes into account spare part lead times, criticality and your maintenance strategy.
This service helps you optimize your inventories. You'll have the best possible availability to recover fast from unexpected events and the right parts and amounts in your inventory.
Shutdown planning and shutdown scope recommendation
Planning maintenance for a huge amount of valves for your upcoming shutdown can be complicated. There are so many things that need to be taken into account in the turnaround scope.
With the help of our dedicated tools for shutdown planning in the Valmet Customer Portal, you can work on the same plan together with our Valmet experts. Our online shutdown planning tool will show all the recommendations and criticality next to your valve position information, making it easy to select the valves that need attention next.
Digital valve audit for installed base and site audit for inventory optimization
All data will lose it’s accuracy with time if not maintained. Same goes for your installed base data. To ensure correct parts and maintenance focus, we offer installed base audits.
As there might be hundreds, or even thousands of valves at your site, it might be laborious to check all the valves in the field. Our digital audit gives you a list of devices where to focus first.
Criticality analysis workshop
Identifying field device condition and maintenance requirements can be challenging. Unplanned maintenance, and unexpected device breakdowns can have a remarkable impact on plant or process uptime, not to mention possible financial impact. By understanding both the process and reliability requirements, and equipment and process criticality, maintenance plans can be established. Through such planning, you can ensure that maintenance and operating costs can be kept at a designated level without jeopardizing reliability.
In criticality analysis workshop our Valmet experts use a powerful template to define criticalities to all valves. After the workshop, you'll get a list of critical tags that can be updated in your system and all the service Valmet provides (shutdown planning, inventory management, installed base) will use the new criticality definition as base information.
Downloads
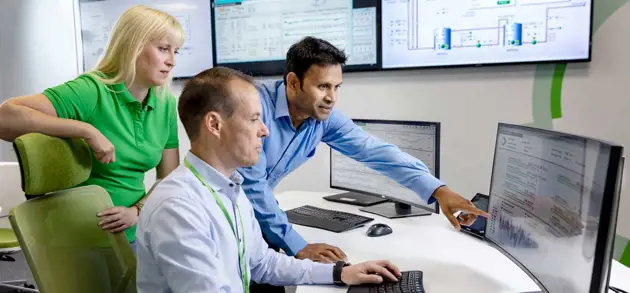
Maximizing valve performance and simplifying life cycle management through digitalization
In this webinar, we will delve into real-world case studies to demonstrate how digitalization can enhance valve performance, streamline life cycle management, and deliver tangible benefits.
Watch the webinar